Optical yarn defects sensor
The yarn defect sensor WeftMaster® FALCON-i is a unique sensor that detects smallest yarn defects, knots and other irregularities in filament yarns and tapes used in various manufacturing processes of high value technical fabrics.
- The optical defect sensor FALCON-i is an important innovation for flawless production of technical fabrics.
- With its autonomous operation and intuitive user interface, the sensor makes it easy to select the desired quality level with just one button.
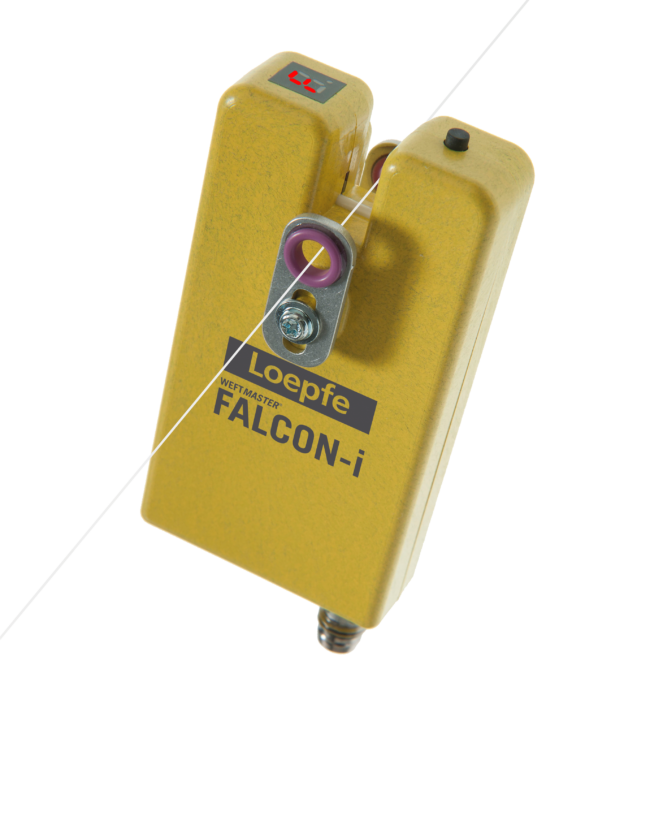
FALCON-i
Removing smallest knots, fluff and filamentation
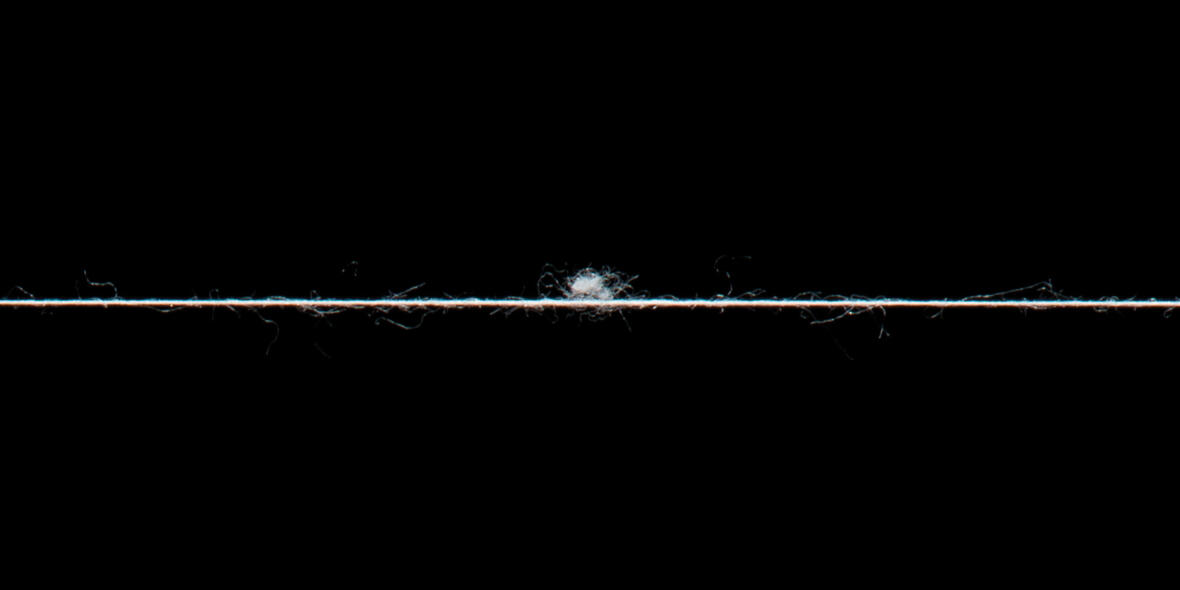
dTex 470: fluff
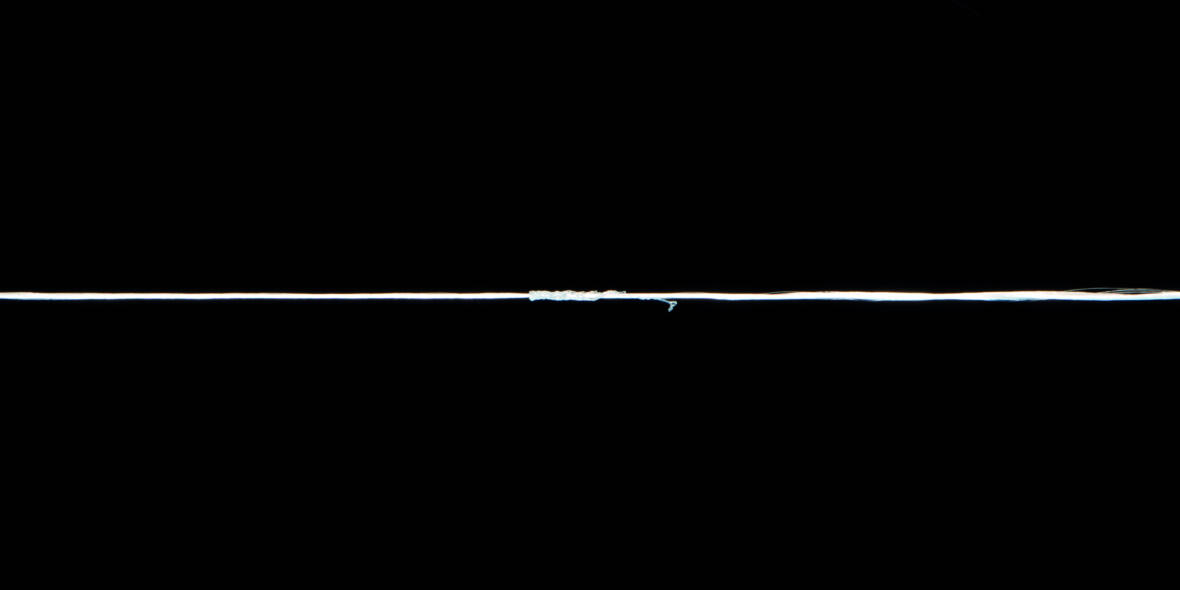
dTex 860: stretch fault
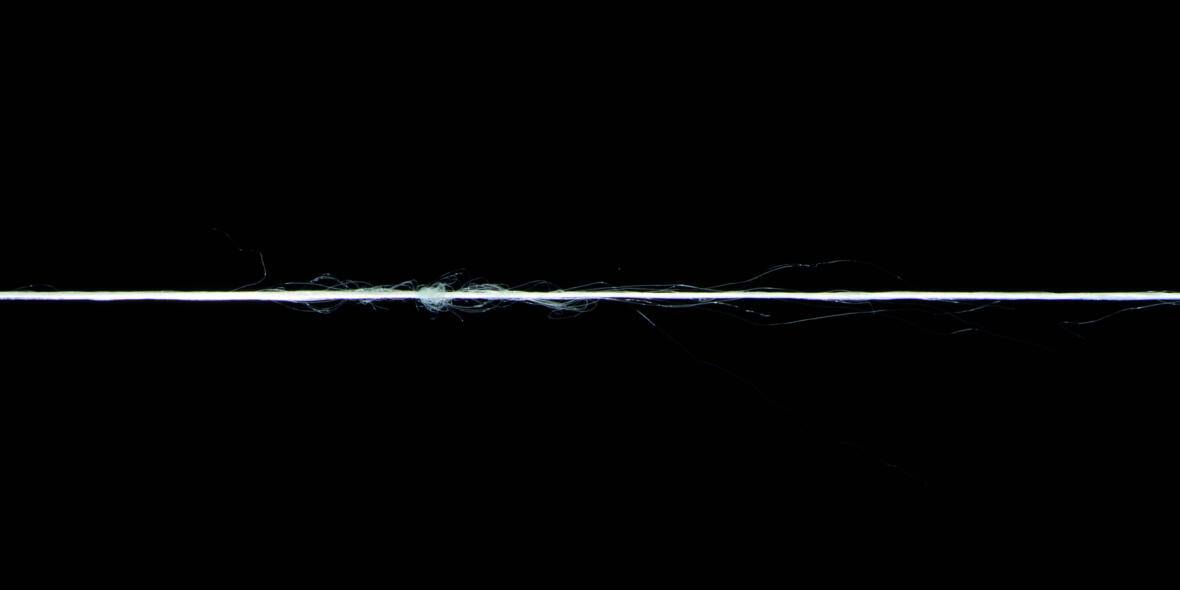
dTex 1100: filamentation
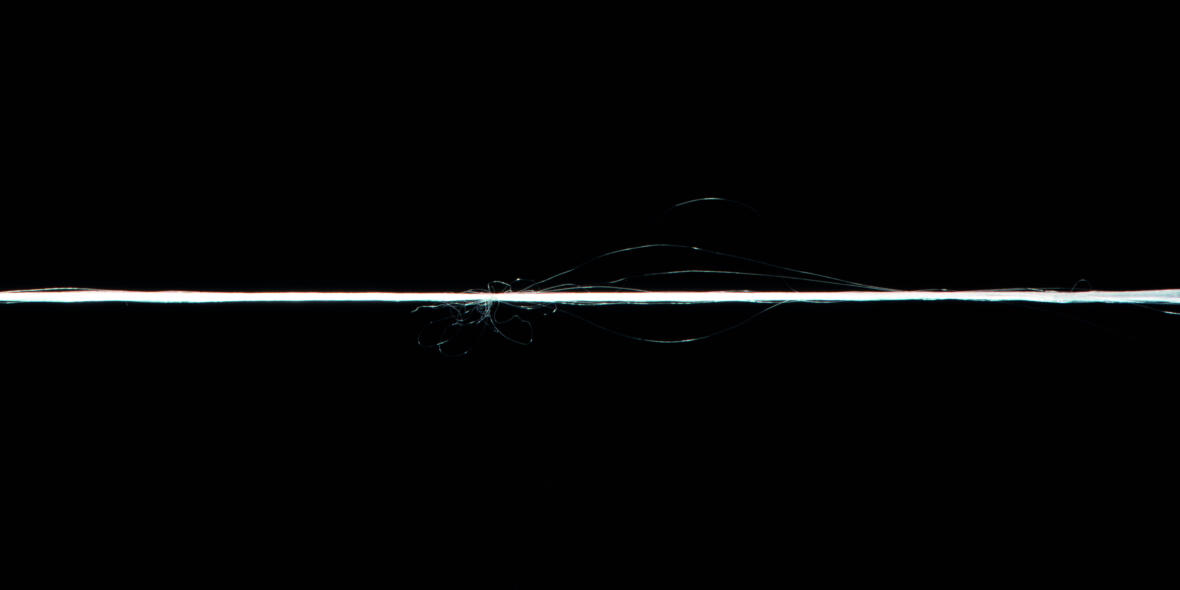
dTex 470: filamentation
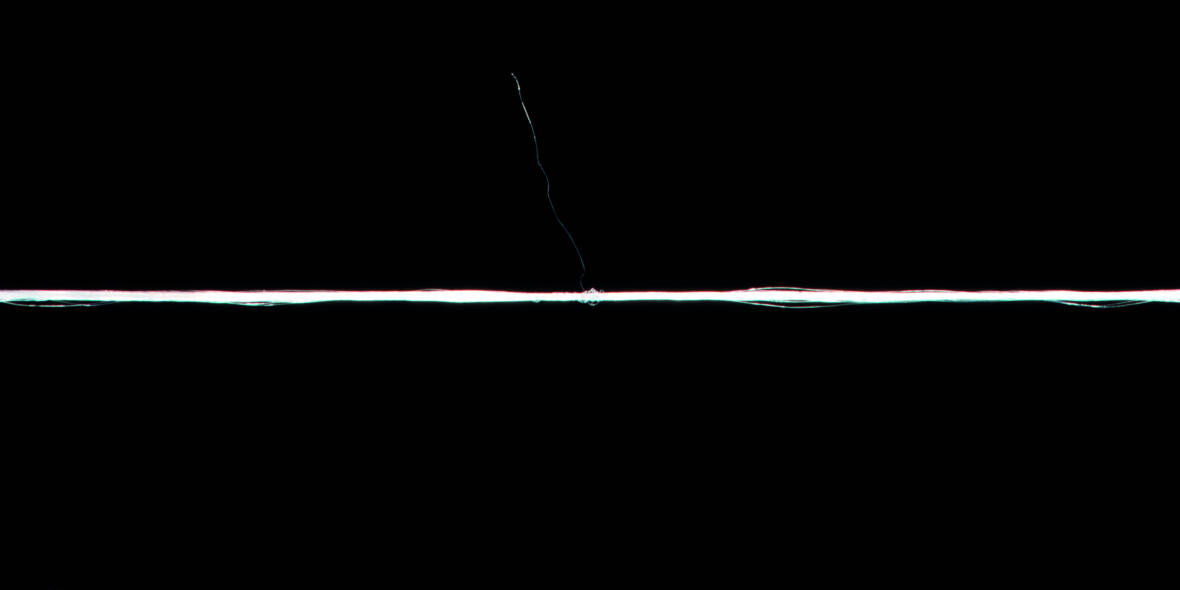
dTex 1100: filamentation
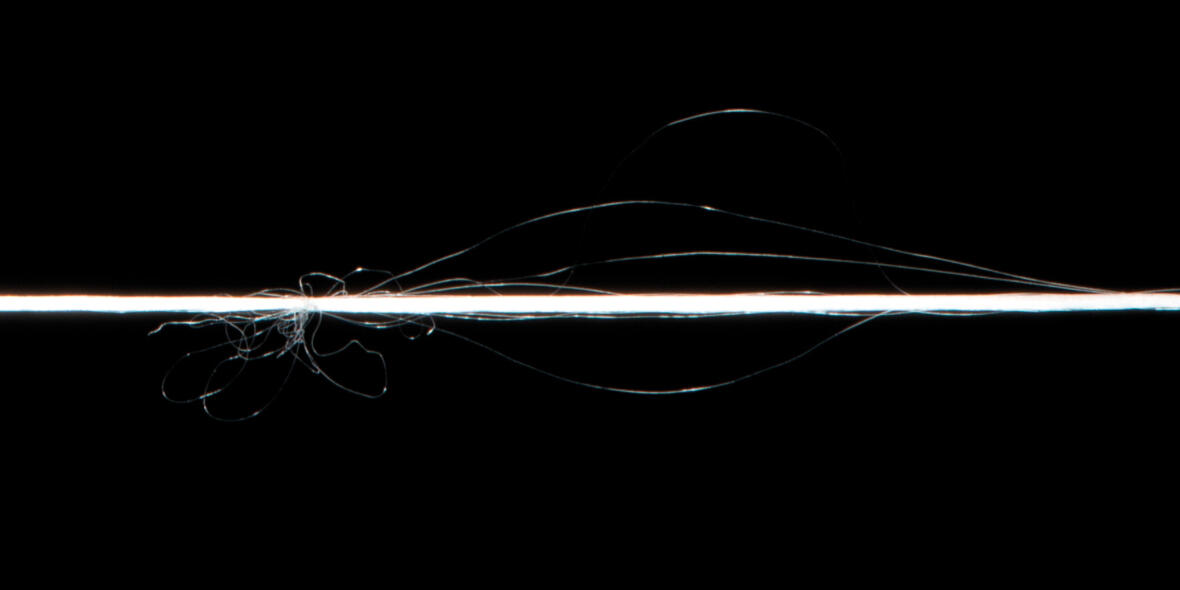
dTex 1100: filamentation
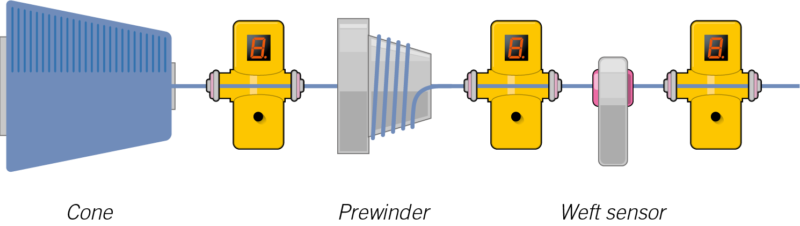
Adaptive quality control
To detect unwanted yarn faults on the running threads, the WeftMaster FALCON-i is installed before or after a weft feeder.
- Between cone and prewinder
Prevents that the knot is erroneously woven. - Between prewinder and weft sensor
Detection of defects which can occur on the prewinder or deflections. - After weft sensor
Detection of defects which can occur on the prewinder, weft sensor or deflections.
Application examples
Discover instances where FALCON-i significantly contributes to a zero-defect manufacturing process for technical textiles. As FALCON-i ensures meticulous control over every millimeter of the yarn, detecting even the smallest defects like knots, fluff, and filamentation. Operating reliably amidst machine vibrations, high speeds (up to 30 meters/second), and diverse yarn types (any color, conductive materials, monofilament or multifilament yarns).
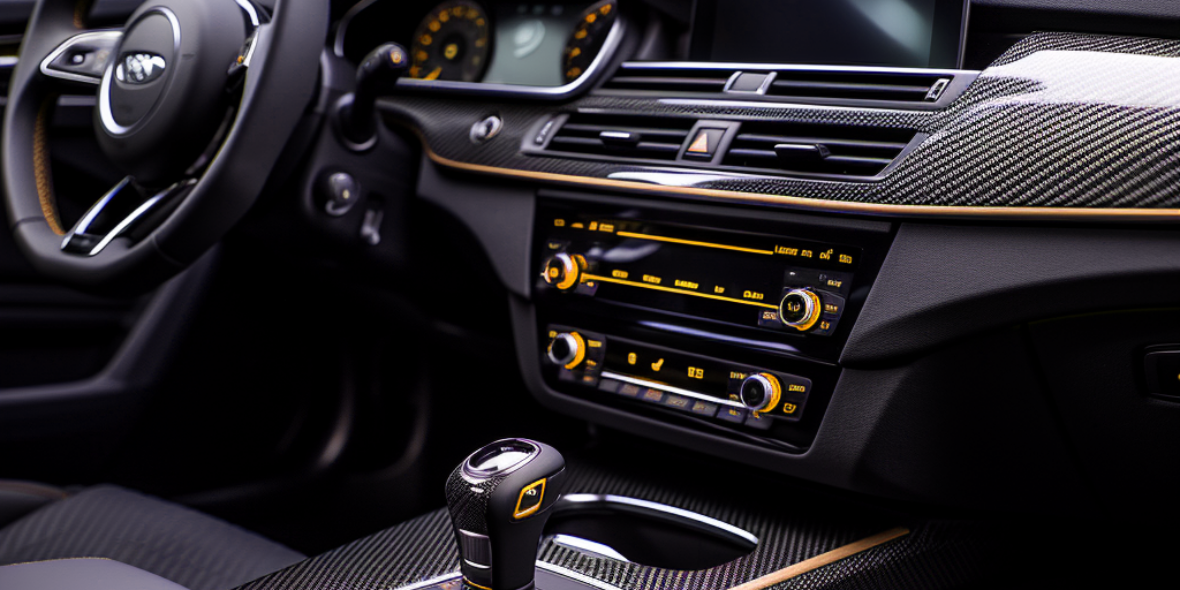
Carbon fabrics
People's concerns about adverse effects from pollution on our living environment is growing. Industries are being forced to reduce their impact on the environment. Transportation accounts for up to one third of all CO2 emissions and cars generate a major share of the pollution. The need to reduce the weight of a car in order to cut its emissions or to increase its range is clear. Steel is getting replaced by carbon fiber based composites and car interiors are being provided with luster by using carbon fabric inlays. The quality of the carbon fabric is crucial for reaching the expected performance.
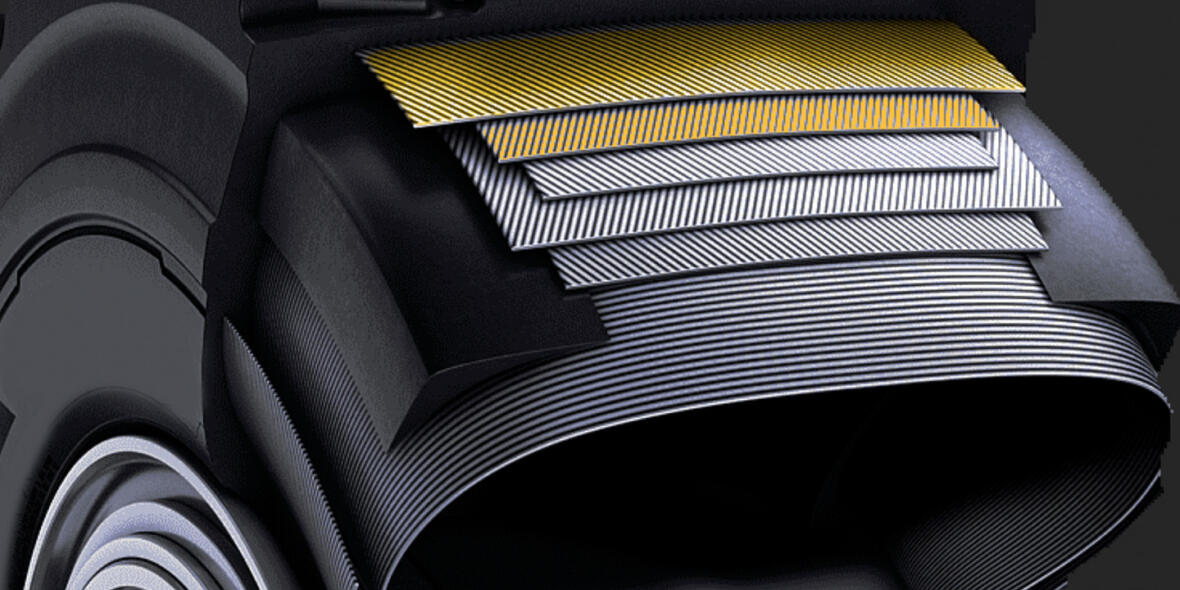
Tire cords
There must be no compromises when it comes to products which affect safety. Car and aircraft tires, as well as high-pressure hoses, must meet the highest quality standards. In the tire manufacturing process, every step of the production is meticulously executed, monitored and controlled. That’s why manufacturers rely on the best control instruments available – so it’s no surprise that they choose the Loepfe WeftMaster FALCON-i, optical yarn defect sensor to support them in this important area.
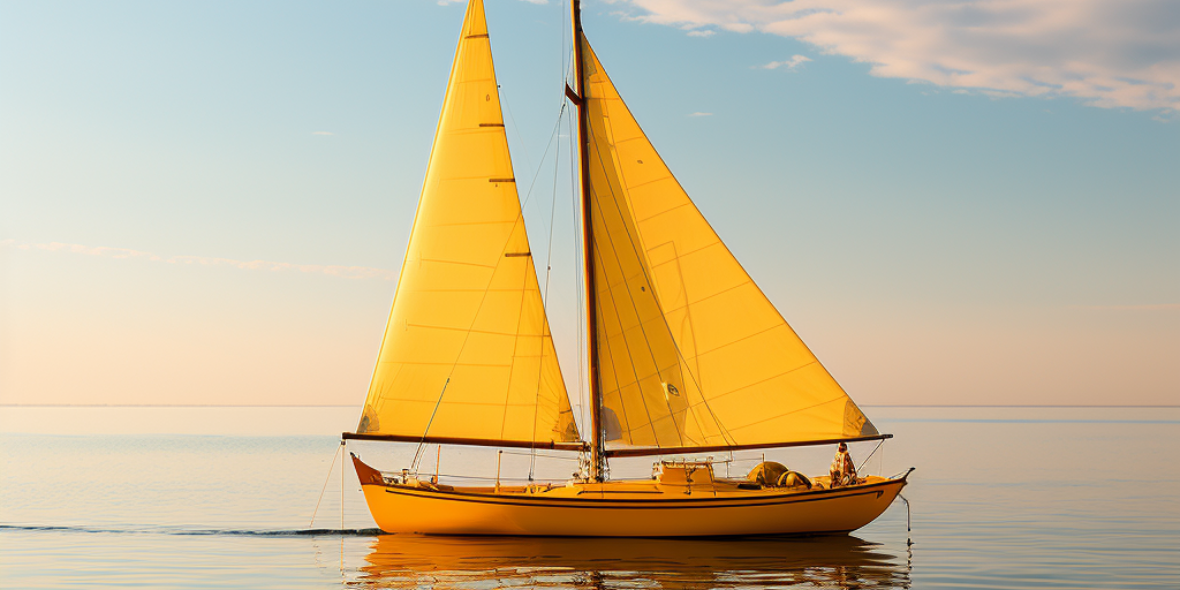
Sailcloth
Wind, water, salt and the highest loads. Sailing is something for true professionals and experts. Likewise making sailcloth, one of the most demanding high-performance fabrics, is produced only by specialized weavers.
A sailcloth must retain its shape even in high winds, but also allow and withstand strong stretching and this over a long period of time. In addition, the fabrics are constantly in contact with water and salt, which additionally stresses their surfaces. A fabric can only sustain these high demands if it has been manufactured to the highest quality.
Submit your data and you will be contacted by one of our experts
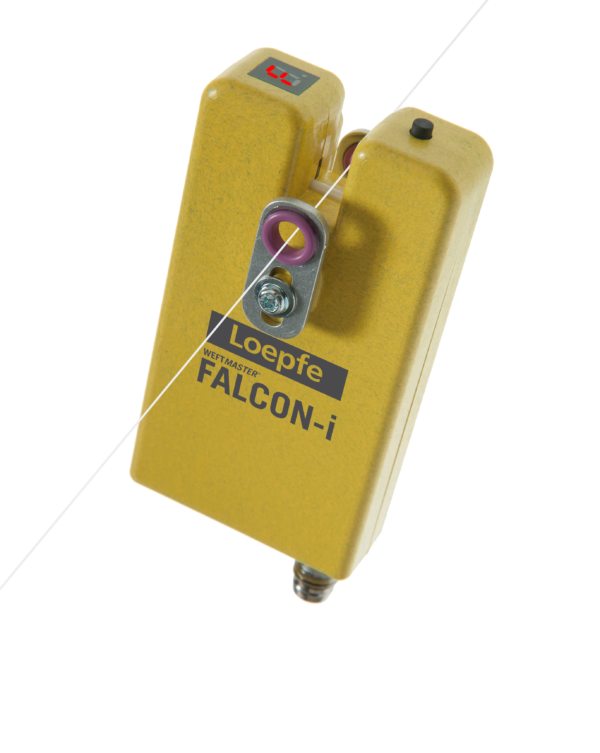