Optisches Inspektionssystem für Kettenwirk- und Raschelmaschinen
Das optische Inspektionssystem ARRAYCAM 5420 ist für die Überwachung von Standardware auf allen gängigen Kettenwirkmaschinen und auf Raschelmaschinen (einfache Musterungen) geeignet. Es besticht durch seine hochwertige Qualität und sein herausragendes Preis-Leistungs-Verhältnis. Die Kontrolle der Wirkware erfolgt mit Präzisionskameras, staubgeschützt in ein Schutzprofil eingebaut, direkt auf der Textilmaschine. Die angebaute LED-Beleuchtung sorgt für eine gleichmäßige Ausleuchtung der Wirkware. Wird ein Fehler erkannt, stoppt die Maschine sofort und der Bereich des Fehlers wird durch einen roten Lichtfleck auf der Ware angezeigt.
- Modular aufgebautes Kamerasystem zur Kontrolle von Wirkware auf Kettenwirk- und Raschelmaschinen (einfache Musterungen)
- Sichere Fehlererkennung mit schnellen Reaktionszeiten
- Einfache Bedienung dank mehrsprachiger Benutzeroberfläche am Steuergerät
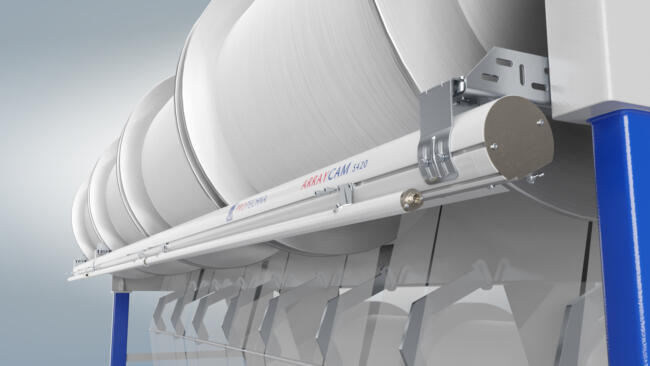
Application examples
Discover instances where FALCON-i significantly contributes to a zero-defect manufacturing process for technical textiles. As FALCON-i ensures meticulous control over every millimeter of the yarn, detecting even the smallest defects like knots, fluff, and filamentation. Operating reliably amidst machine vibrations, high speeds (up to 30 meters/second), and diverse yarn types (any color, conductive materials, monofilament or multifilament yarns).
Carbon fabrics
People's concerns about adverse effects from pollution on our living environment is growing. Industries are being forced to reduce their impact on the environment. Transportation accounts for up to one third of all CO2 emissions and cars generate a major share of the pollution. The need to reduce the weight of a car in order to cut its emissions or to increase its range is clear. Steel is getting replaced by carbon fiber based composites and car interiors are being provided with luster by using carbon fabric inlays. The quality of the carbon fabric is crucial for reaching the expected performance.
In the case of inlay-components with a carbon look, even the smallest irregularities are a problem. Hence, carbon fabrics must have controlled quality to avoid sporadic defects. Weavers of carbon fabrics who are working closely together with car manufacturers don’t take any risks - they rely on Loepfe's FALCON-i to keep fluff or filamentation out of their top quality fabrics.
By using the unique detection features of Loepfe's FALCON-i yarn sensor to remove fluff or filamentation from the weft-yarn, waste is dramatically reduced in the carbon fabric production process. A simple calculation reveals that there’s a quick return on investment for the weaver.
The applications where FALCON-i can improve product quality are not limited to those mentioned here. Coated technical fabrics such as tarpaulins or sailcloth can only be perfect when using FALCON-i for weaving the base material, in order to avoid fish-eye defects.
Weavers with a focus on high quality technical textiles benefit from using the unique detection capabilities of FALCON-i to improve the quality of their products while avoiding customer claims or expensive patching.
FALCON-i offers selectable sensitivity levels to cope with many different applications. Since the sensor is optical, the nature or conductivity of the yarn processed is of minor importance. Smooth yarn guidance allows for very selective fault sensitivitysettings.
This specialized yarn sensor product from Loepfe Switzerland is in high demand for the production of technical textile fabrics that find their application in automotive, medical, aeronautics, filtration, recreational sports, renewable energy - and many other industries too.
Sailcloth
Wind, water, salt and the highest loads. Sailing is something for true professionals and experts. Likewise making sailcloth, one of the most demanding high-performance fabrics, is produced only by specialized weavers.
A sailcloth must retain its shape even in high winds, but also allow and withstand strong stretching and this over a long period of time. In addition, the fabrics are constantly in contact with water and salt, which additionally stresses their surfaces. A fabric can only sustain these high demands if it has been manufactured to the highest quality.
Loepfe products are used in a wide range of industries to ensure zero-defect manufacturing and production efficiency, this is also the case for sailcloth production. Loepfe's WeftMaster FALCON-i, WeftMaster KW and WeftMaster SFB products perform important quality control functions during production to ensure the high quality desired. Another Loepfe product from the WeftMaster series, the WeftMaster CUT-iT, is also integrated into the manufacturing process to ensure perfect selvedges and smooth further processing.
So, why do well-known manufacturers of sailcloth rely on all these Loepfe products?
First and foremost, the FALCON-i sensor prevents faulty yarn from being woven into the fabric in the first place. As before the yarns are woven into fabric, an all-round control over every single millimeter of the running yarn is applied by FALCON-i, as the high-tech yarns must be completely free of even the smallest knots, fluff and filamentation. The FALCON-i optical yarn defect sensor detects such defects in the yarn completely reliably – and is unaffected by the strong vibration caused by the weaving machine, the high speed (yarn speed up to 30 meters/second) and the yarn to be monitored (any color, conductive materials, monofilament or multifilament yarns). Such a high-performance fabric can only be produced with reliable quality control - as every defect is a possible weak point that can lead to poor performance or a shorter lifecycle.
However, the sensor also contributes massively to production efficiency as up to 90% of machine downtimes can be attributed to weft faults. Weft faults arise largely due to production-related defects and irregularities in the yarn. In the weaving process for technical fabrics - made from multifilaments – filamentation, individual fibril breaks, fluff or the smallest knots in the weft yarn are a problem. The detection of flaws in the weft yarn prevents defective fabrics and expensive complaints. For reliable monitoring and efficient defect detection, the FALCON-i sensor is mounted in front of the weft feeder.
Additionally, the masters of their trade attach great importance to perfect selvedges as sailcloth requires specialized finishing methods to withstand the stresses. They know that only perfect selvedges can ensure smooth further processing, as well as preventing coating machines from severe wear. Thus, manufacturers rely on the WeftMaster CUT-iT to get perfectly cut synthetic fabrics. CUT-iT is the ideal fabric cutter system for thermal cutting of thin, light-to-dense and heavy synthetic fabrics. CUT-iT guarantees at all times precise performance even at fast machine starts and stops with its intelligent cutting temperature control for constant high-quality output in the weaving mill.
Loepfe, through its latest technology products, is proud to be a part of this whole process - and acknowledges with admiration the great skill and dedication of the expert weavers who produce such high-performance fabrics! And to all sailors out there “may you have fair winds and following seas".
Versions
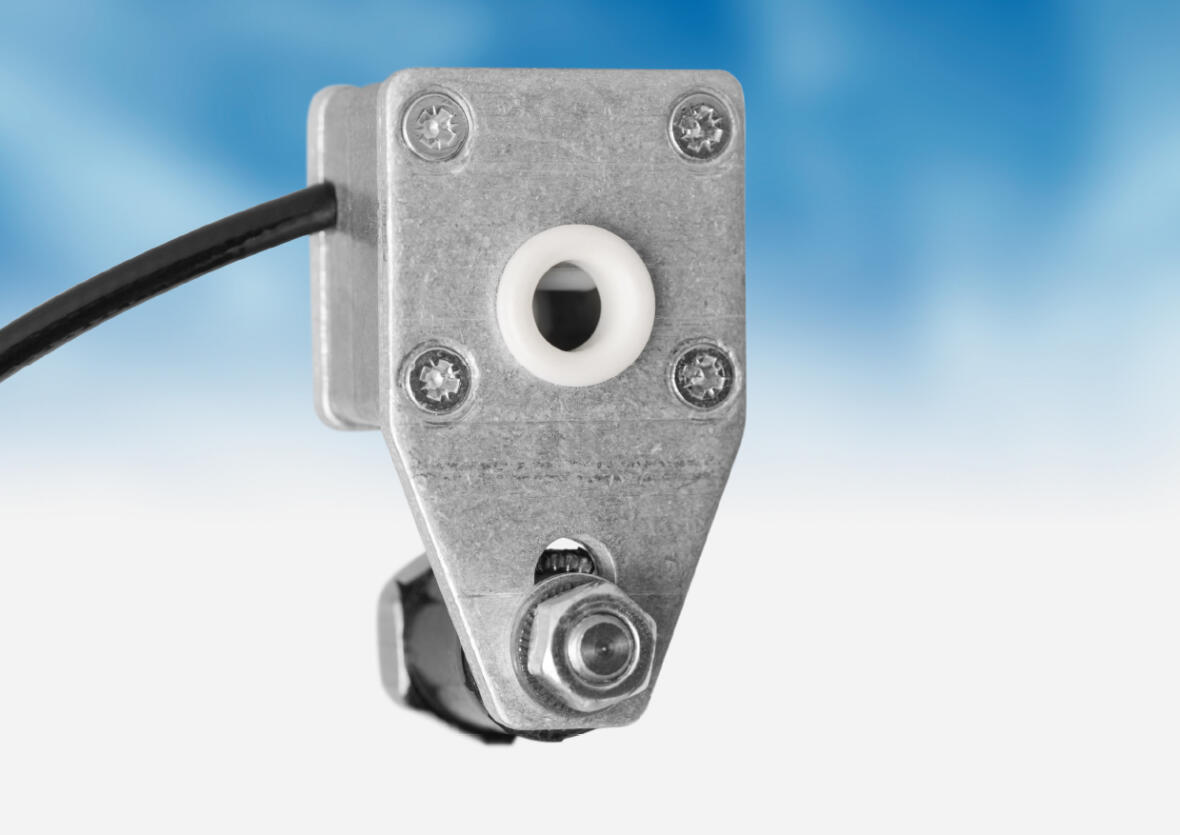
For projectile weaving machines
WeftMaster SFW-L Mini
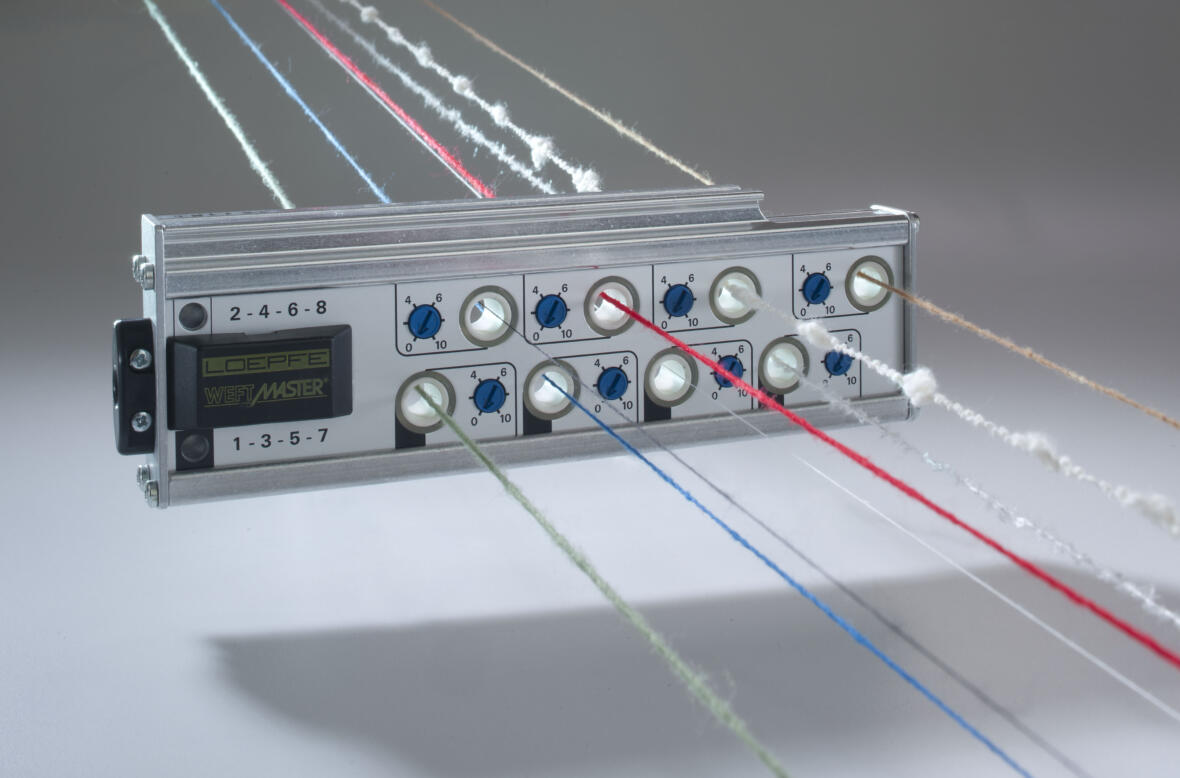
For rapier weaving machines
WeftMaster SW 10G
Geben Sie Ihre Daten ein und einer unserer Experten wird sich mit Ihnen in Verbindung setzen.
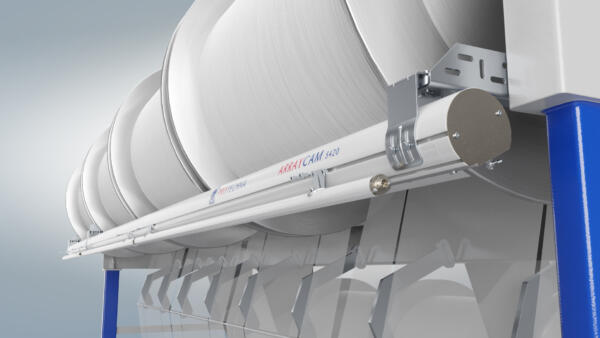